Aqua feed pellet mills are essential in producing high-quality feed pellets for fish, shrimp, and other aquatic species. Among the key components of these mills, the ring die plays a crucial role in determining pellet quality, production efficiency, and machine durability.
What Is a Ring Die?
A ring die is a circular, perforated metal component in a pellet mill where feed material is compressed and extruded into pellets. It works in conjunction with rollers that press the feed mixture through the die holes, shaping it into uniform pellets.
Key Components of a Ring Die
Die Holes (Compression Channels) – Determine pellet size and shape.
Effective Thickness – Influences compression and pellet density.
Inlet & Outlet Conical Design – Affects material flow and extrusion efficiency.
Material Composition – Typically made from high-chromium alloy steel for wear resistance.
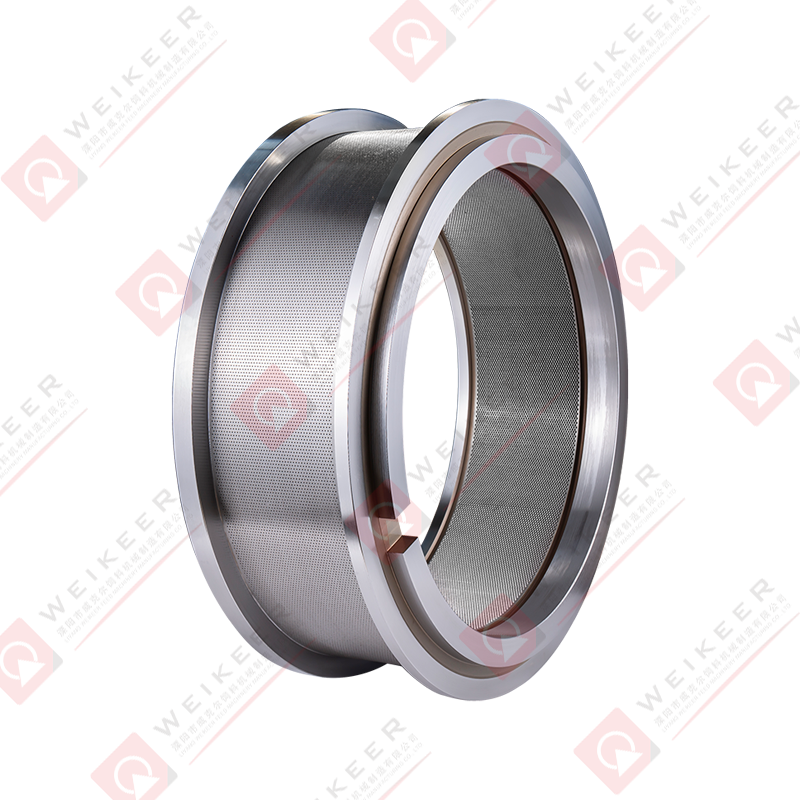
The Role of the Ring Die in Aqua Feed Pellet Production
1. Pellet Formation and Shaping
The primary function of the ring die is to shape the feed mixture into uniform pellets. As the rollers press the mash feed against the die, the material is forced through the die holes, forming cylindrical pellets.
Die Hole Diameter: Determines pellet size (e.g., 1.5mm–8mm for different fish species).
Compression Ratio (L/D Ratio): Affects pellet hardness and durability.
2. Controlling Pellet Density and Durability
The compression thickness of the ring die influences pellet density:
Thicker Dies → Higher compression → Denser, harder pellets (better for sinking feed).
Thinner Dies → Lower compression → Softer pellets (suitable for floating feed).
3. Influencing Production Efficiency
Die Hole Pattern & Open Area: Affects throughput and energy consumption.
Wear Resistance: High-quality dies last longer, reducing downtime.
4. Impact on Feed Digestibility and Water Stability
Properly designed dies ensure pellets have optimal water stability, preventing rapid disintegration in water.
Smooth extrusion reduces heat damage, preserving nutritional value.
Design and Material Considerations for Ring Dies
1. Die Hole Configuration
Straight vs. Step Holes: Step-hole dies improve pellet durability.
Tapered Inlet & Outlet: Reduces friction and energy consumption.
2. Material Selection
High-Chromium Alloy Steel (20CrMnTi, 42CrMo): Offers high wear resistance.
Stainless Steel (SS420, SS440): Used for corrosive aqua feed ingredients.
Carbide-Enhanced Dies: For extended lifespan in high-abrasion conditions.
3. Surface Treatment & Hardening
Heat Treatment (Quenching & Tempering): Enhances hardness (HRC 55-60).
Nitriding or Chrome Plating: Improves corrosion resistance.
Common Issues & Maintenance of Ring Dies
1. Wear and Tear
Uneven Wear: Leads to inconsistent pellet quality.
Corrosion: Caused by high-moisture or salty feed ingredients.
2. Preventive Maintenance Practices
Regular Cleaning: Prevents clogging from residual feed.
Proper Lubrication: Reduces friction between rollers and die.
Periodic Rotation: Ensures even wear distribution.
3. Signs of a Worn-Out Ring Die
Increased power consumption.
Poor pellet formation (crumbling pellets).
Visible erosion around die holes.
Comparison Between Ring Die and Flat Die Pellet Mills
Feature |
Ring Die Pellet Mill |
Flat Die Pellet Mill |
Pellet Quality |
High-density, uniform pellets |
Less consistent density |
Production Scale |
Large-scale (5-30+ T/H) |
Small-scale (0.1-3 T/H) |
Energy Efficiency |
Higher efficiency |
Lower efficiency |
Maintenance Cost |
Higher initial cost |
Lower initial cost |
Ring dies are preferred in large-scale aqua feed production due to their superior pellet quality and efficiency.
The ring die is a critical component in aqua feed pellet mills, directly influencing pellet quality, durability, and production efficiency. Proper material selection, die hole design, and maintenance are essential for optimizing performance and extending the die’s lifespan.
For aquaculture feed producers, investing in high-quality ring dies ensures better pellet stability, improved digestibility, and lower operational costs in the long run. By understanding its role and implementing best maintenance practices, manufacturers can maximize output while maintaining high feed quality standards.
Future Trends in Ring Die Technology
Advanced Coatings: Nano-coatings for longer durability.
AI-Assisted Wear Monitoring: Predictive maintenance using IoT sensors.
Customized Die Designs: Optimized for specific feed formulations.
As aquaculture continues to grow, advancements in ring die technology will further enhance feed pellet production efficiency and sustainability.